For more information on accessibility, access procedures and deadlines, see our Training page.
9S or 8D in Aerospace-Defense: analysis and problem-solving methods – #87
Context
You want to :
- Improve the efficiency of your groups in charge of solving internal problems and handling customer complaints.
- Strengthen the facilitation skills of your 9S or 8D leaders.
- Identify the risks at each stage of 9S or 8D.
- Anticipate customer requirements concerning the conformity of your approach to the EN 9136 standard or RM 13000.
Objectives
- Show the benefits of an approach in accordance with EN 9136 and RM 13000.
- Understand the 9 steps and the importance of each step.
- Practice using the method and tools associated with the different phases.
- Know how to lead a working group.
Recommanded for
- Quality teams
- Quality / QHSE managers, engineers and technicians
- Production managers
- Purchasing managers
- Group facilitators
Prerequisites
No prerequisites.
Pedagogy
- After a theoretical presentation, participants work in sub-groups to understand and appropriate the steps and tools of the 9S/8D method step by step.
- The trainees are put in turn in a facilitator’s situation throughout the training, in order to reinforce their skills in facilitating work groups; certain sequences are the subject of a specific debriefing on the facilitation techniques.
- Each sequence is illustrated by numerous exercises and the application of a case study.
- Each of the 9 stages of the process ends with the presentation of the RM 13000 assessment grid.
Evaluation mode
- Knowledge test (MCQ).
Course materials
-
Participant file containing the presentations delivered during the training and the exercise materials.
To go further
Trainings :
- Becoming a Green Belt – #61
- The TRIZ method: Theory of Inventive Problem Solving – #116
- Knowing and mastering the impact of human factors – #759
Consulting services : EURO-SYMBIOSE can assist you in the concrete implementation in your company. Contact us to know more about it.
Introduction to the problem-solving approach: feedback, objectives.
Terms and definitions: different types of actions, different types of causes.
From the traditional approach to problem-solving methodology
When to use the 9S methodology.
Step 0 – Start immediate containment actions
Step 1 – Building the team.
Step 2 – Define the problem.
Step 3 – Complete and optimise conservation actions.
Step 4 – Identify the root causes.
Step 5 – Define and select corrective actions.
Step 6 – Deploy corrective actions and check their effectiveness.
Step 7 – Standardise and transfer knowledge.
Step 8 – Acknowledge the team and close.
A summary of the approach and tools.
Pitfalls and traps.
QRQC, a field management dynamic.
Laurent LUX - AD PAMIERS
“The first day, which was theory-oriented, enabled me to brush up on the methodology that I thought I knew… It was during the second day’s practical application that I really realised all the pitfalls, shortcuts and lack of questioning that can lead to a poor analysis. Great training”.
Eric VAN PATTEGHEM - ERAMET
“Very interesting training with concrete situations that allow a good understanding of the tool presented. “
Edouard ROMACHO - ERAMET
“Dynamic training allowing us to question ourselves without denigrating past work. A lot of interaction”.
Alexandre LACOMBRADE - ERAMET
“The content was very interesting, very dynamic. “
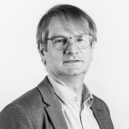
Register several trainees for our Open training sessions and benefit from our special offers