Infos
VDA 19.2 – Technical cleanliness in assembly
- 27 November 2019
- Posted by: Stagiaire Communication
- Category: Actuality
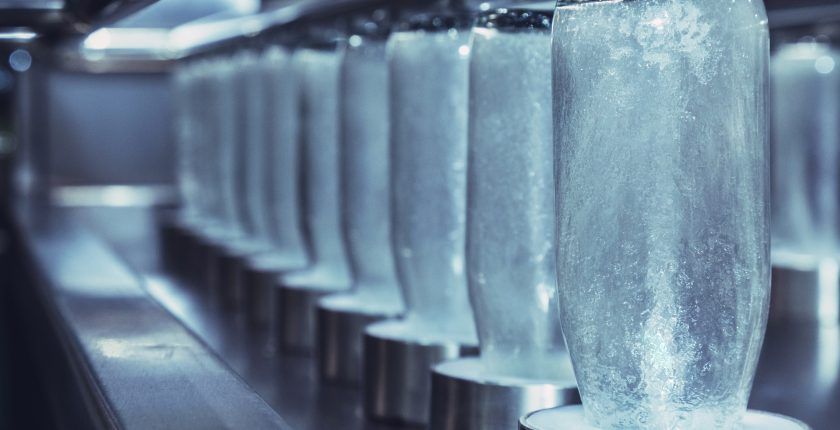
VDA 19.2 is a good practice guide, originally inspired by the medical and chemical sectors, to identify, analyse and control sources of contamination. Among the multitude of parts that make up a vehicle, some are more susceptible to contamination from dust or foreign objects.
This applies particularly to mechanical systems with fluid circulation with or without pressure (braking / steering / fuel supply / cooling / air conditioning systems), intake / exhaust ducts, manual / automatic transmission, but also to electronic control units.
As a result of the development of electric mobility, VDA 19.2 also covers vision systems, batteries and fuel cells and high-voltage electronics.
This pollution that occurs during the manufacture of parts is often difficult to detect with the naked eye (e.g. wood or metal particles), but it can be enough to create a critical failure in the final product. A 50 micron particle can limit the circulation of fluids, create motor malfunctions, disturb electrical functions, and even lead to motor failure!
Example of a particle in an injector
The VDA 19.2 guide recommends, depending on the customer’s requirements and the use of the product, the measures to be taken upstream (e.g. adapting the packaging to protect the components during transport), during manufacture (e.g. orienting the open components downwards to limit the introduction of particles) and after manufacture (e.g. positioning rubber stoppers to avoid any migration of contamination inside the component) to limit or even eliminate all sources of pollution.
Fuel filter component
It is necessary to think globally and to carry out an analysis of the risks of contamination over the entire life cycle of the product in order to find the most appropriate solutions for the company’s context. The risk analysis is carried out station by station and consists of
- Identifying the most polluting operations;
- Organising the layout of workstations to distance/isolate the source of pollution from the rest of the process;
- Finding a solution for the most risky workstations.
These cleanliness requirements must be incorporated into the design of new workstations to avoid contamination.
The guide identifies 4 potential sources of pollution:
- Environment = Linked to external pollution (e.g. doors often open, dusty workstations, etc.).
- Logistics = Linked to packaging (e.g. cardboard versus plastic).
- Personnel = Human (ex: hair).
- Means of production = Linked to the equipment (e.g. dirty machines).
The more sensitive the product, the more specific the procedure to follow.
The value of VDA 19.2
Volume 2 of VDA 19 describes a series of analytical and test procedures for determining the cleanliness of environments, surfaces, liquids and assembly processes. The procedures can be used to :
- Identify and quantify sources of particulate matter to derive improvement measures and validate their effectiveness.
- Identify weak points in an operating manufacturing facility in order to determine optimisation potentials to be incorporated when planning a new facility.
- Monitor processes or areas over a long period of time.
Finally, VDA 19.2 complements VDA 6.3, as a VDA 6.3 auditor can also audit the requirements of VDA 19.2.
â–º Find out about the 2-day training course to become a Skilled Assistant 19.2.