Infos
The place of people in the Lean of today… and tomorrow
- 26 March 2019
- Posted by: Stagiaire Communication
- Category: Actuality
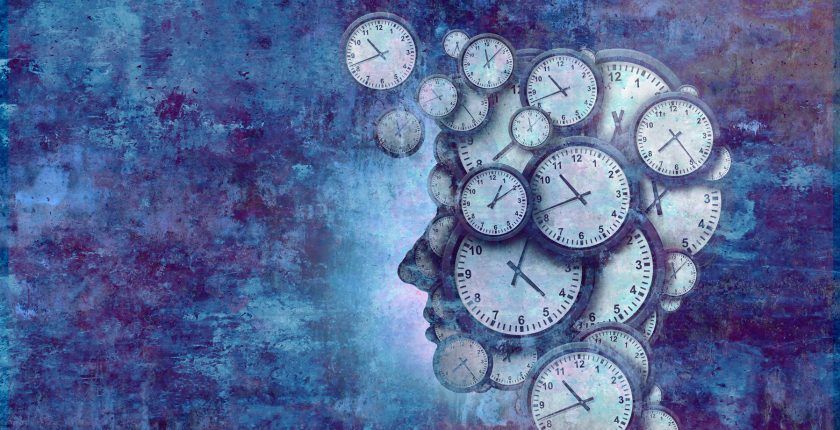
Â
Editor : Laurent HERNANDEZ, Lean and industrial management expert.
 A month ago, Iproposed a comparison between the Lean of yesterday and tomorrow, deliberately omitting to mention the Human. This new article is intended to be exploratory on the place of Man in Lean organisations, a basis for reflection rather than a postulate on the definition of your needs in terms of necessary transformations, both organisational and individual and personal.
First of all, let us remember that Lean, apart from is theoretical or operational aspects on production processes, is also and fundamentally based on a philosophy of continous improvement, Kaizen (kai: “change”, zen: “best”). In the history of Lean, this philosophy places the human being at the heart of the system, particularly in the notion of autonomy (ability to deal with problems, to reorganise as accurately as possible, etc.), self-management of situations (visual management, reactivity, etc.) in a spirit of permanent learning, in order to achieve “perfection” (5th principle of Lean thinking). Communication and collaboration are at the heart of the Lean organisation. They lead people to understand, to dismantle the “mechanisms”, to explain how they work, to draw the practical consequences, to make diagnoses and to propose action and improvement plans. Lean is above all a formidable vector for managing change and people, and transforming the culture of companies in a sustainable way.
In its TPS, TOYOTA has long valued people more than machines. People learn every day to enrich their experience, at all levels of the organisation, by contributing to the know-how accumulated to improve the system, whereas machines are intended to be depreciated and then ultimately replaced.
Ergonomics: “The scientific study of the relationship between man and his means, methods and working environment, and the application of this knowledge to the design of systems “which can be used with maximum comfort, safety and efficiency by the greatest number of people” (cf. Wikipedia). This definition is itself rooted in Lean thinking, in the spirit of the TPS (Toyota Production System), when it comes to thinking and working on improving the performance of an organisation, by reducing MUDA (waste), MURI (variability) and MURA (overload). Lean is undoubtedly linked to this notion, and aims in some way to make our organisations more ‘ergonomic’, adaptable, flexible and sustainable.
Before moving forward on this place in the organisations and industries of the future, it’s essential for each organisation to reflect on and diagnose the real, operational and effective place that it has given to people in the management of its performance.
What about tomorrow ? One might think that in the ‘’company of the future’’, man will disappear in favour of a computerised, robotic, autarkic system thanks to an over-developed artificial intelligence. These fears are of course founded on the trend of the last industrial revolutions. They always lead to the idea that humans will be « replaced ».However, this idea remains too global, too generic, too restrictive. Let us recall what was said above. It is true that some operations are and will be better performed by robots (their reliability and flexibility are constantly evolving) and algorithms. The fact remains that as long as a computer system is not capable of autonomously solving different problems with the flexibility of trained and motivated workers and technicians, production will continue to be based on humans. All the means mentioned in my reflection on Lean 4.0 remain tools for improving certain global or operational performances (communication, cobotisation, object intelligence, etc.) but require and will necessarily require human intervention. The above definition of ergonomics, associated with Lean, should “simply” make us think about this relationship between Man and his future new means. Lean Management and Lean Design are at the forefront of this reflection.
Depending on the field, many professions will be affected by this 4th industrial revolution. The role of the human being will be affected both quantitatively and qualitatively. New ways of working on added value will bring with them a need for additional, complementary knowledge and skills. Simply “downsizing” is not the issue in these revolutions. The notion of the workforce (the relationship between the quantification of human resources at any level of the organisation chart) has always been the subject of reflection, decisions, adjustments, strategic or operational and day-to-day developments. It will continue to be so and deserves to be anticipated. This anticipation will necessarily involve work on the “jobs of tomorrow” and, above all, on the management of the organisations’ skills.
To conclude, it is certain that the philosophy and operational aspects of Lean will evolve with new technological means. Its foundations, based resolutely on the very grassroots and human approach, will nonetheless remain relevant. The participative approach inscribed in the Lean doctrine could potentially be a possibility for operators to “control” the prescription system by having a major role in their configuration, reconfiguration and improvement. Let us take the example of Lean managerial approaches such as QRQC (Quick Response Quality Control), which aim to remain anchored in reality, transversal collaboration and reactivity. The collection of data (Big data) and its processing or the interaction with AI will not make them obsolete, quite the contrary. The new tools available will make it possible to make faster comparisons, easier statistical processing, and reduce lead times, but they will never take away the need to be creative, responsive, and collaborative, as close as possible to the added value and the field. The challenges of the place of Man in the ergonomics of the companies of the future must be thought out and imagined today in order to be successful tomorrow. They will necessarily involve an improvement in the quality of work and an increase in skills at all levels. Their operational deployment will perhaps make it possible to put people at the heart of a system where their ideas, creativity and ability to mobilise skills in the right place at the right time will be put forward. Diagnosing and understanding the components of the performance of one’s organisation are now becoming really necessary.