Infos
Become a green belt lean, an involvement beyond performance improvement
- 30 October 2019
- Posted by: Stagiaire Communication
- Category: Actuality
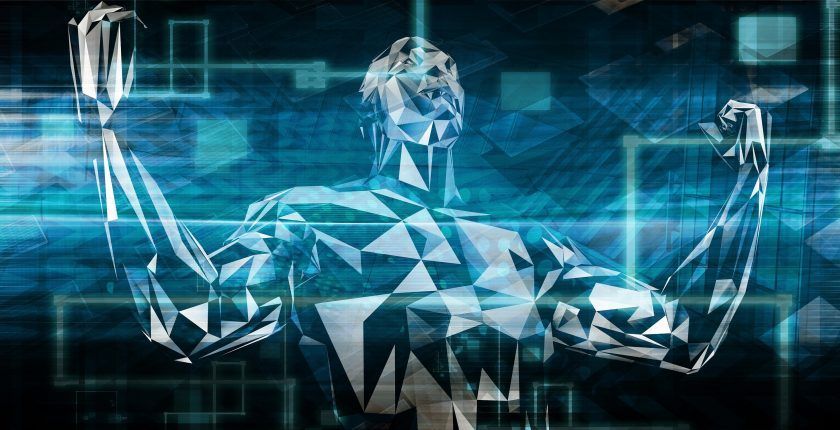
Editorial: Laurent HERNANDEZ, lean and industrial management expert.
Learning and understanding the applied concepts of Lean is a good start. Each Lean tool and approach can be appreciated independently of the others, depending on the issues that an organization needs to address. But approaching the improvement of the performance of a department, a process (administrative or productive), from a more global point of view, with a step back and a vision of the potentials, is a very different issue.
What does it mean to be a certified Green Belt in Lean (Office or Manufacturing)? What knowledge, skills and learning methods? What missions and what assignments are open to you on a daily basis?
This is what I propose to discover in this article.
The AFNOR NF XO6-091 standard of 2011 has proposed, for the Lean and Six Sigma domains, an approach in terms of competency management, with a reference framework allowing to see more clearly. I will use its content to continue our discovery of the scope of capabilities offered by the Green Belt Lean certification.
From a knowledge point of view, a Green Belt first acquires the means to model and measure the efficiency of his working environment (tasks, flows, organization) by learning to think about added value, in all types of industries, service companies and even in design.
- Learn to identify the added value by analyzing the flow, losses and waste, use the Value Steam Mapping to map the physical flows, information, stocks and connections between all actors in the system …;
- To be able to analyze the capacity of a post, the efficiency of the work cycles, to balance the tasks and to develop the flexibility of a service, of a production island;
- Understand standardization as a real asset, serving the performance as well as the well-being of an organization, carry out real 5S projects and propose solutions to gain not only in quality, costs and details, but also in safety and motivation ;
- Implement visual performance management, specific animation rituals according to needs, but also work on improving flows, reducing stocks (physical or virtual) by applying simple or intermediate tools such as SMED, Kanban, FIFO and the Milkman System.
These are all skills that the Green Belt will be able to apply.
The Green Belt in Lean
To become a Green Belt in Lean (Office, Manufacturing, Design) is to be able, with practice, to :
- Perceive more easily what can separate a production team and/or a department from the performance it seeks to achieve;
- Devote a part of their working time to improvement through breakthroughs (implementation of a specific project);
- Understand the concepts and tools of Lean management that facilitate the realization of daily improvements on processes, while promoting teamwork;
- Become a major player in the organization, capable of leading real transformation projects in line with the strategic alignment of an entity, and in the service of results that are always measured;
- Putting people at the heart of the system. To make the organization and the people who work in it grow by highlighting potential, understanding the issues, selecting the appropriate tools and implementing them collectively.
Today, all sectors of activity are developing their organization and their human resources in order to acquire this Lean vision. Lean tools and Green Belts are the main actors, for a better future.